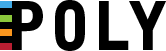
Le Magazine de Polytechnique Montréal
Rouler sur la Lune
Grand dossier
Le 17 novembre 1970, pour la première fois, un véhicule roulait sur le sol lunaire : Lunakhod, l’astromobile-robot déposée par une sonde soviétique. À partir de l’année suivante, ce fut au tour de la NASA de faire rouler son rover LRV sur la Lune dans le cadre de ses missions Apollo. Les prochaines missions lunaires, qui prévoient des séjours prolongés sur l’astre rocheux, impliquent le développement de nouveaux types de rovers mieux adaptés à l’environnement hostile de la Lune. Souhaitant contribuer à cette nouvelle étape de la conquête spatiale, le Pr Daniel Therriault, directeur de la Chaire Safran-Polytechnique sur la fabrication additive des composites à matrice organique (FACMO), dirige une équipe multidisciplinaire de chercheurs et de partenaires industriels vouée à la conception d’un rover lunaire fabriqué en composites thermoplastiques.
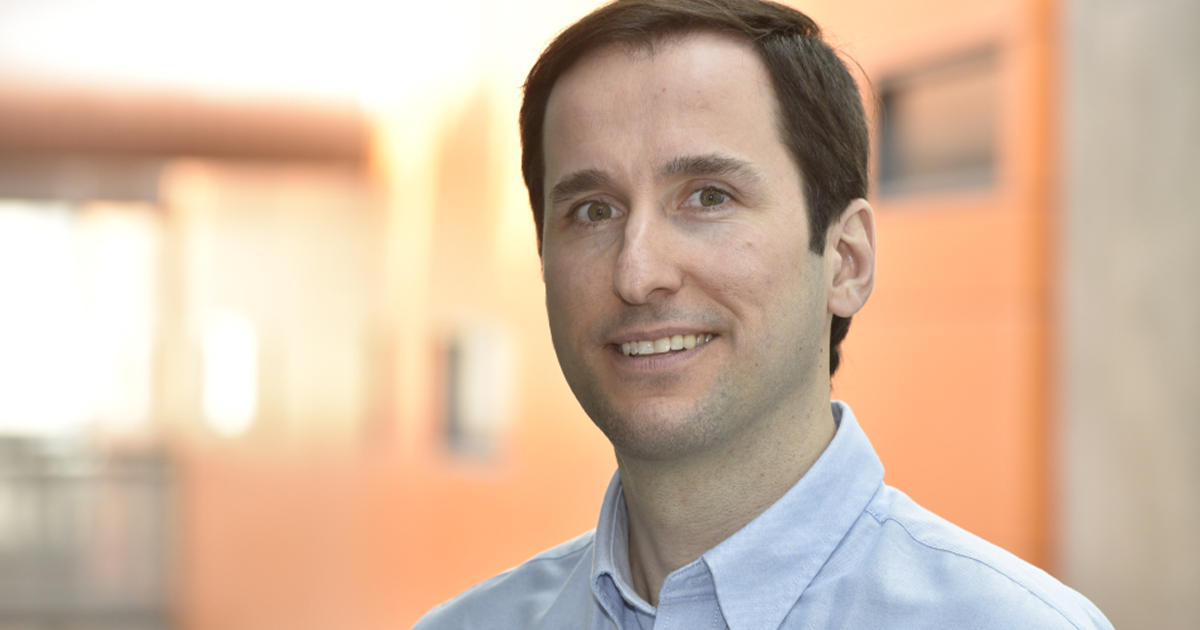
(Photo : Caroline Perron)
Un projet qui a pris de l’ampleur
« À l’origine, l’idée a été lancée par Marie-Josée Potvin, ingénieure principale des systèmes à l’Agence spatiale canadienne, dont un des mandats est de développer des véhicules de type rover capables de réaliser des missions sur le sol lunaire », mentionne Daniel Therriault. L’Agence spatiale canadienne travaille sur ces véhicules depuis une douzaine d’années, en collaboration avec des entreprises canadiennes, mais jusqu’à présent, ses projets se concentraient essentiellement sur les technologies de télécommunications et d’instrumentation, c’est-à-dire sur la réalisation d’antennes, du système de navigation et de capteurs. Les prototypes étaient montés "à l’ancienne", à partir de structures métalliques tenues ensemble par des vis, écrous et boulons. Or, outre le problème du poids de cet assemblage, se pose celui de son endurance dans les conditions extrêmes du milieu lunaire. « Le temps est venu de s’intéresser à la structure du véhicule, en explorant les performances des matériaux composites et de nouvelles façons de procéder à l’assemblage de ses différentes parties. »
Pour réaliser ce projet, 10 professeurs ont joint leurs expertises : le volet conception de nouveaux matériaux est pris en charge par Basil Favis et Nick Virgilio, tous deux du Département de génie chimique de Polytechnique, et Éric David, du Département de génie mécanique de l’ÉTS; les procédés de fabrication sont mis au point par Daniel Therriault et Frédérick Gosselin (fabrication additive), ainsi que Louis Laberge Lebel (pultrusion), tous trois du Département de génie mécanique de Polytechnique; la soudure par induction des pièces imprimées en 3D est étudiée par Jason R. Tavares, du Département de génie chimique de Polytechnique, et Martine Dubé, du Département de génie mécanique de l’ÉTS; le volet modélisation pour la prédiction des performances de la structure est, quant à lui, réalisé par Martin Lévesque, du Département de génie mécanique de Polytechnique, et Marie-Laure Dano, du Département de génie mécanique de l’Université Laval. Enfin, Daniel Therriault, Martine Dubé et Louis Laberge Lebel s’occupent également de l’aspect intégration des systèmes et de l’assemblage du rover.
« Notre projet a démarré en 2018, avec une subvention de 50 000 $ provenant de CREPEC Vision, un programme du Centre de recherche sur les systèmes polymères et composites à haute performance (CREPEC) visant à encourager l’exploration d’idées originales manquant d’un soutien industriel. Ce financement relativement modeste, renouvelé l’année suivante, nous a permis de recruter des étudiants et de produire des idées prometteuses de design et de matériaux et ensuite de recevoir l’appui financier de partenaires comme Ariane Group et NanoXplore, fournisseur de graphène, en plus de la contribution scientifique de l’Agence spatiale canadienne. Nous bénéficions également de l’expertise des PME québécoises Dyze Design, un fabricant d’accessoires haute performance pour l’impression 3D, et Mëkanic, un fournisseur d’équipement de recherche sur mesure. Notre équipe a, de plus, reçu cette année le soutien du programme CRSNG Alliance et de Prima Québec, si bien que nous bénéficions maintenant pour les quatre prochaines années d’un financement de 727 095 $, dont 327 623 $ provenant du Ministère de l’Économie et de l’Innovation par l’intermédiaire de PRIMA Québec, ce qui va nous permettre d’engager encore plus d’étudiants des cycles supérieurs ainsi que des stagiaires postdoctoraux », précise le Pr Therriault.
Un rover nommé PEEKbot
Le projet de rover de l’équipe du Pr Therriault est baptisé PEEKbot, en raison du thermoplastique haute performance appelé PEEK (poly[étheréthercétone]), autorisant l’assemblage par induction (un procédé de soudure électrique) qui est utilisé pour le développement de sa structure. La longueur de celle-ci ne dépassera pas un mètre, ce qui représente une taille moyenne pour un rover lunaire. Actuellement, l’équipe travaille sur la réalisation du châssis, la plus longue pièce horizontale et la plus complexe de leur prototype.
« La structure cellulaire de cette pièce est bio-inspirée. En effet, à l’instar d’un tissu osseux, la densité et la taille des cellules variera en fonction de la sollicitation mécanique : le matériau sera plus compact à l’endroit où il sera le plus sollicité, et plus léger aux autres endroits. Nous avons développé une méthode de calcul pour parvenir à optimiser la densité de cette structure poreuse, et gagner en légèreté », indique le Pr Therriault, qui a mis à contribution pour l’impression du matériau le système robotisé de son laboratoire, employé habituellement à la fabrication de revêtements acoustiques pour la Chaire Safran-Polytechnique.
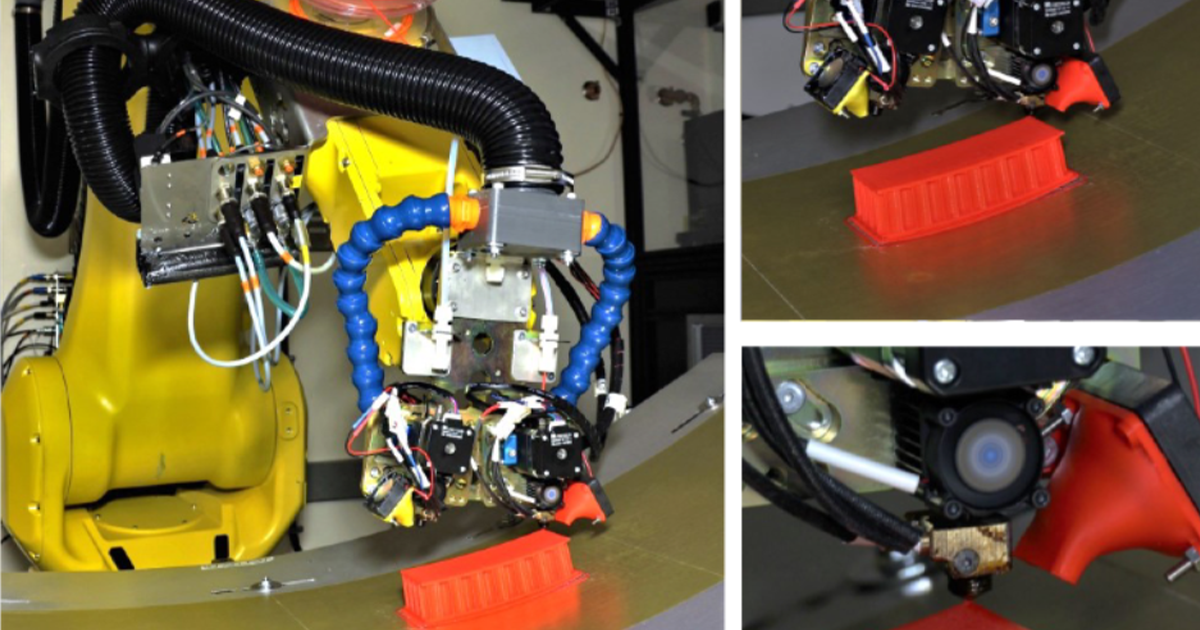
Essais de fabrication additive (images fournies par Daniel Therriault)
Certaines pièces du PEEKbot ne pourront pas être assemblées par induction. L’équipe a donc prévu de fabriquer également des vis, boulons et écrous dans le même composite. « Sur la Lune, les grandes variations de température amènent les matériaux à se dilater et à se contracter très fortement. Or, des éléments fabriqués dans des matériaux différents le feront à des amplitudes et vitesses différentes, ce qui engendrera des contraintes importantes et donc des bris, ce que l’on souhaite éviter », explique Daniel Therriault.
Autre défi : léger et résistant mécaniquement, le matériau doit aussi être peu conducteur de chaleur, car, pour préserver les batteries, il faut limiter au maximum les pertes d’énergie thermique durant la nuit lunaire, qui dure 14 jours terrestres, où la température tombe sous -150 oC. « Il faut, en outre, tenir compte des poussières abrasives recouvrant le sol lunaire et qui pourraient endommager la structure du rover, ou encore se coller sur les panneaux solaires qui l’alimentent, poursuit le Pr Therriault. Une dégradation accélérée pourrait aussi être causée par les radiations. Ce sont des aspects que nous étudions également dans l’analyse de performance de notre matériau. »
Durant la troisième année du projet, l’équipe a prévu de travailler à l’intégration des diverses composantes du rover et d’y ajouter des roues en vue d’aller faire des essais sur le sol de simulation lunaire de l’Agence spatiale canadienne.
Inspiré par Neil Armstrong
Conception de matériaux à hautes performances, nouveaux procédés de fabrication, modélisation… Ce projet stimule le développement d’un vaste champ de nouvelles connaissances et ouvre la voie à de nombreuses applications dans des domaines terrestres. « Comme ces matériaux sont conçus pour des conditions extrêmes, on peut envisager de les employer dans l’environnement nordique. Ils pourraient notamment aider à répondre à certains enjeux des communautés du Grand Nord », souligne le Pr Therriault.
Celui-ci, qui avait autrefois souhaité être astronaute, confie être allé célébrer le 50e anniversaire des premiers pas de l’Homme sur la Lune au Musée national de l'air et de l'espace, à Washington, juste devant la combinaison spatiale de Neil Armstrong. « Si un système réalisé par notre équipe de recherche était un jour expédié sur la Lune, ce serait l’accomplissement d’un de mes plus grands rêves de carrière. »