Blogue
When the circus comes to... the lab!

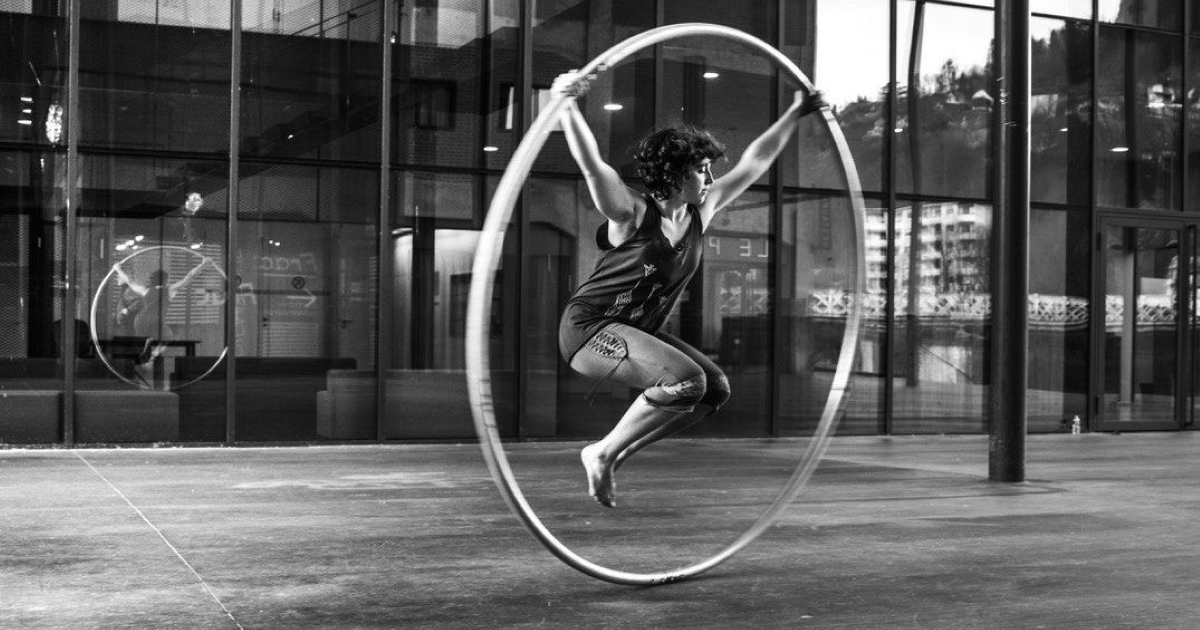
Charlotte Dubost (photo : Anne-Marie Lambert-Chevrier)
When Charlotte Dubost decided on a rather unconventional subject for her Master’s degree in engineering, she approached a handful of professors on both sides of the Atlantic. The result? Polytechnique Montréal Professor Frédérick Gosselin was quick to open his lab’s doors to her. This is the story of a circus artist / graduate student who decided to bring a touch of engineering genius to a made-in-Québec circus tool: the Cyr wheel.
Charlotte Dubost arrived in Montréal with a rather ambitious project in mind: to spark a revolution – so to speak – in the small community of Cyr wheel users. Also known as a mono wheel, the approximately two-metre-diameter tool is used by circus performers - including Dubost herself - for acrobatic routines.
“It’s a really interesting tool, but one that has limitations because of its rigidity and weight, which can be up to 20 kilograms,” the France-born artist / engineer explains. “I thought that if we replaced the metal with a composite material, we could make the wheel more compressible, for example, and greatly expand the range of what’s technically possible for performers.”
In recent years, composite materials (or composites) made partially of carbon fibre have come into their own because of their lightweight nature that’s at once both flexible and strong. Composites are common in aircraft and automobile components, as well as in bicycle frames and tennis rackets, among other applications. Even the laptop computer with which this article was written is partly clad in composites.
The wave of composites adoption also came ashore in the circus arts world, Dubost says. For example, they’re now being used to build trapeze frameworks, and Chinese pole performers are taking advantage of these highly flexible materials to push the latter apparatus to its limits.
Chinese pole structures are made using long straight composite fibre rods straight from the factory, with minor modifications. However, as the young researcher explains, building a composite Cyr wheel had other challenges: “The designers first had to determine the optimum materials to use, but also had to develop an entire strategy for manufacturing curved pieces with short fibre lengths,” she says.
The short story of... the cyr wheel |
Trained at the National Circus School in Montréal and a member of the Cirque Éloize troupe, Angelica Bongiovonni is one of many contemporary artists who've helped popularize this circus tool. (Photo: YouTube) The Cyr wheel was invented in 2003 by Québec's Daniel Cyr, who is also the co-founder of Cirque Éloize. Custom-made for its user, each wheel is roughly two metres in diameter and is usually made of five arcs of metal (either steel or aluminum) that nest together to form a whole. The Cyr wheel differs from the so-called German wheel, which itself is formed by two wheels connected by bars, like a circular ladder. The latter wheel was patented in 1925 by Otto Feick, who, you might have guessed, was a German national. |
towards a prototype
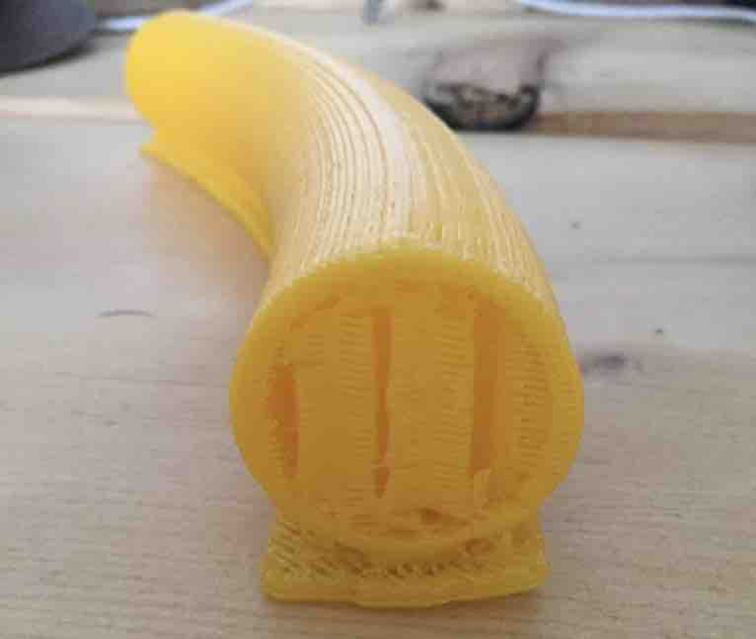
The test printing of a PLA tube which is supported by an internal structure of PVAc (Photo: Charlotte Dubost)
Before moving on to the prototype stage, a number of questions had to be answered. Under the supervision of Professor Gosselin, as well as Professors Annie Ross and Daniel Therriault, the acrobat-engineer conducted a series of tests in silico, digitally modelling Cyr wheel behaviour in various situations.
“We studied two specific motion types - jumps and rotations - and also considered the maximum stress that a Cyr wheel can be subjected to. We now know exactly how a wheel will behave in the real world, regardless of its dimensions or composition,” Dubost comments.
Equipped with the aforementioned information, the researchers then assessed various wheel manufacturing strategies using composites, all based on additive manufacturing (i.e., 3D printing). “Polytechnique has developed impressive expertise in manufacturing composite components using 3D printing,” Dubost notes.
The Polytechnique team eventually settled on using three nesting sections of tubing that form a wheel when assembled. The approach is the same as is used for a traditional metal Cyr wheel, and allows the apparatus to be broken down for easy transportation.
enter the lm2 fanuc robot
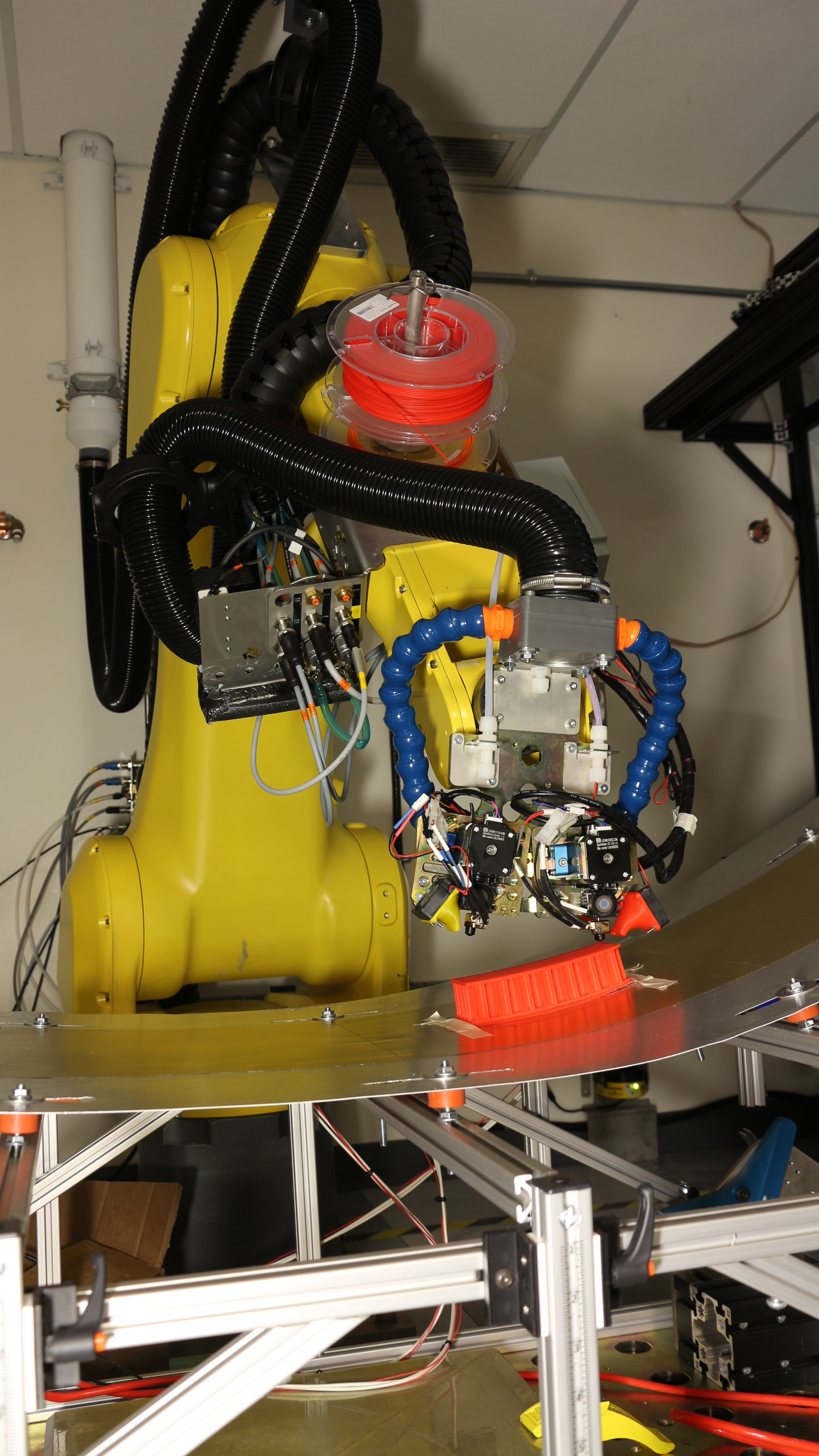
The FANUC robot (Photo : LM2)
After testing three strategies for 3D-printing composites, the research group made its choice, opting for an approach that employs two types of materials. The tube itself will be manufactured using nylon, and will be reinforced during printing with short carbon fibres supported by segments of polyvinyl acetate (PVAc). “This method takes longer than others that we tested, but it allows us to manufacture tubes with high fidelity. Once the piece is finished, we simply put it into water to dissolve the PVAc,” Dubost explains.
In part because of COVID-19, the project hit a series of snags that kept the master’s student from seeing it through to completion. “The most important part is still to come,” she admits, though she’s satisfied with her progress so far.
“We had planned to print the prototype using the FANUC robot [at the Laboratory for Multi-scale Mechanics, or LM2] and we were going to conduct a series of tests and artistic research with the people at the National Circus School in Montréal – which would have been fantastic,” she adds.
Dubost submitted her master’s thesis last December. Will the project restart at some point? Professor Gosselin isn’t ruling it out, but a source of funding would need to be found first.
SPOTLIGHT ON... COMPOSITE MATERIALS |
![]() ![]() Carbon-based composite materials are a blend of at least two types of materials. (Photo : Racingjeff, licence CC 3.0) A material is said to be “composite” when it comprises at least two immiscible components with complementary properties that lend the whole properties superior to the components themselves. One such example is reinforced concrete. When concrete is allowed to set around steel armature, the resulting material gains strength and resistance; neither the “bare” concrete or the steel alone has all these properties when used solo. However, these days the term “composite materials” (or “composites”) typically refers to polymer-based composite materials. Reinforcing carbon or glass fibres are combined with a plastic resin that acts as a binder which distributes stresses across the fibres. The resulting material is often lighter and more flexible than metal, but just as tough and durable, if not more so. Resins made from thermoset plastics or thermoplastics are used in aerospace manufacturing. In the case of both plastics, components are baked in a mould and retain their shape once they cool. |
Learn more
Professor Frédérick Gosselin’s expertise
Professor Daniel Therriault's expertise
Laboratory for Multi-scale Mechanics's (LM2) website
Department of Mechanical Engineering's website
Comments
Commenter
* champs obligatoire