Blogue
Autopsy of a bridge

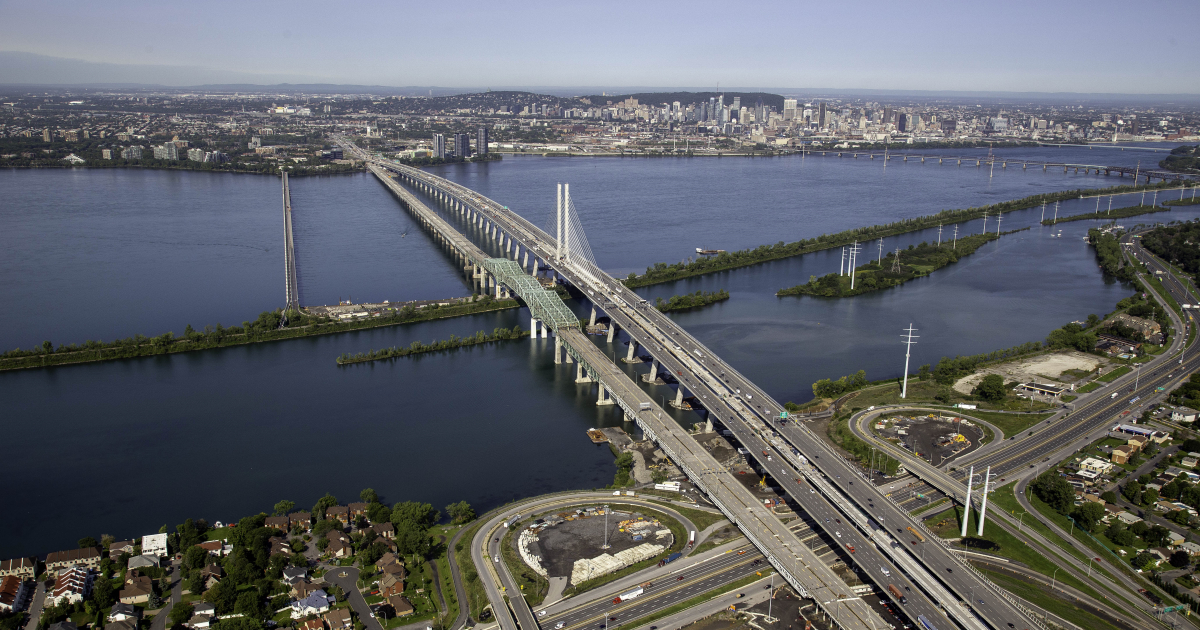
Before disappearing entirely from Montréal’s skyline, the “old” Champlain Bridge will reveal a few of its secrets. (Photo: JCCBI)
In the shadow of the new Samuel-De Champlain Bridge, workers have been busy since last autumn dismantling its older sibling, the Champlain Bridge. Yet the legacy structure will share a few final secrets before it disappears altogether - at least that’s the hope of a Polytechnique Montréal team that’s keenly interested in the demolition. Over the next few months, their laboratory will be receiving 10 or so slabs from the “old” bridge, which will be used to assess state of degradation, and to test repair methods.
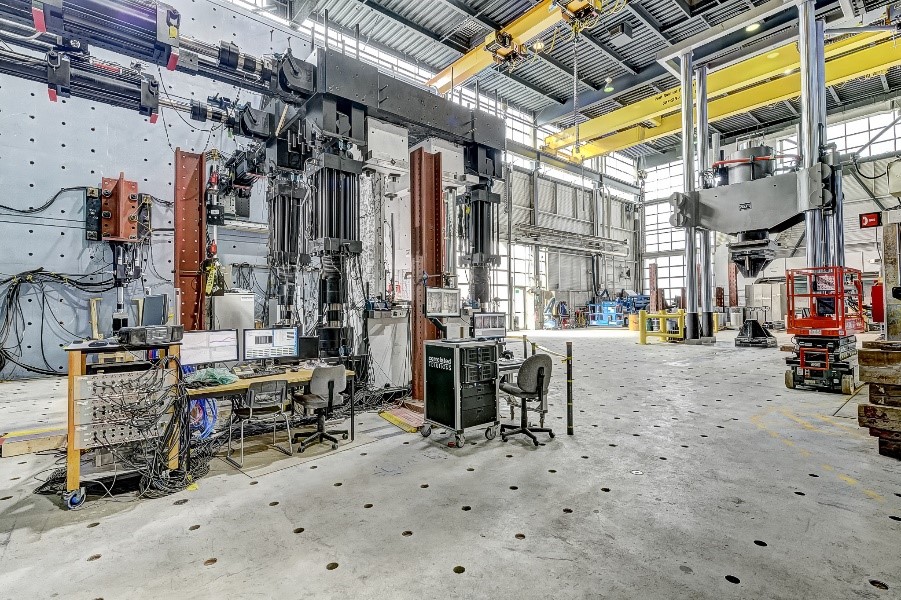
Most of us can’t wait for summer to finally arrive. Yet at Polytechnique Montréal, few people are as excited about it as Jean-Philippe Charron and Mahdi Ben Ftima, two professors from the Department of Civil, Geological, and Mining Engineering who also work at the Centre de recherche sur les infrastructures béton - CRIB.
A few weeks from now, the Polytechnique Structural Laboratory, will be taking delivery of a first of several sections of the old bridge; approximately 10 slabs measuring about 4 metres by 2 metres and weighing some 6 tonnes each, round out the total.
Before vanishing forever, the original Champlain Bridge will enjoy a second life of sorts: some of its constituent materials will be reused or recovered, and others will provide research teams the chance to work with materials and structural elements that are more than a half-century old. In 2019, bridge manager Champlain and Jacques Cartier Bridges Inc (PJCCI) initiated a grant program to collect research and development proposals. Its objective: to take advantage of the Champlain Bridge’s deconstruction to conduct research projects on multiple issues such as degradation, durability, and innovative methods to evaluate and strengthen certain elements of the existing bridge. The project proposed by Polytechnique’s Professors Charron and Ben Ftima was selected by PJCCI.
“We have an outstanding opportunity available to us. We don’t often get the chance to test infrastructure components with this degree of wear and tear in a laboratory setting,” says a visibly enthused Professor Charron.
Inspecting concrete to better repair it
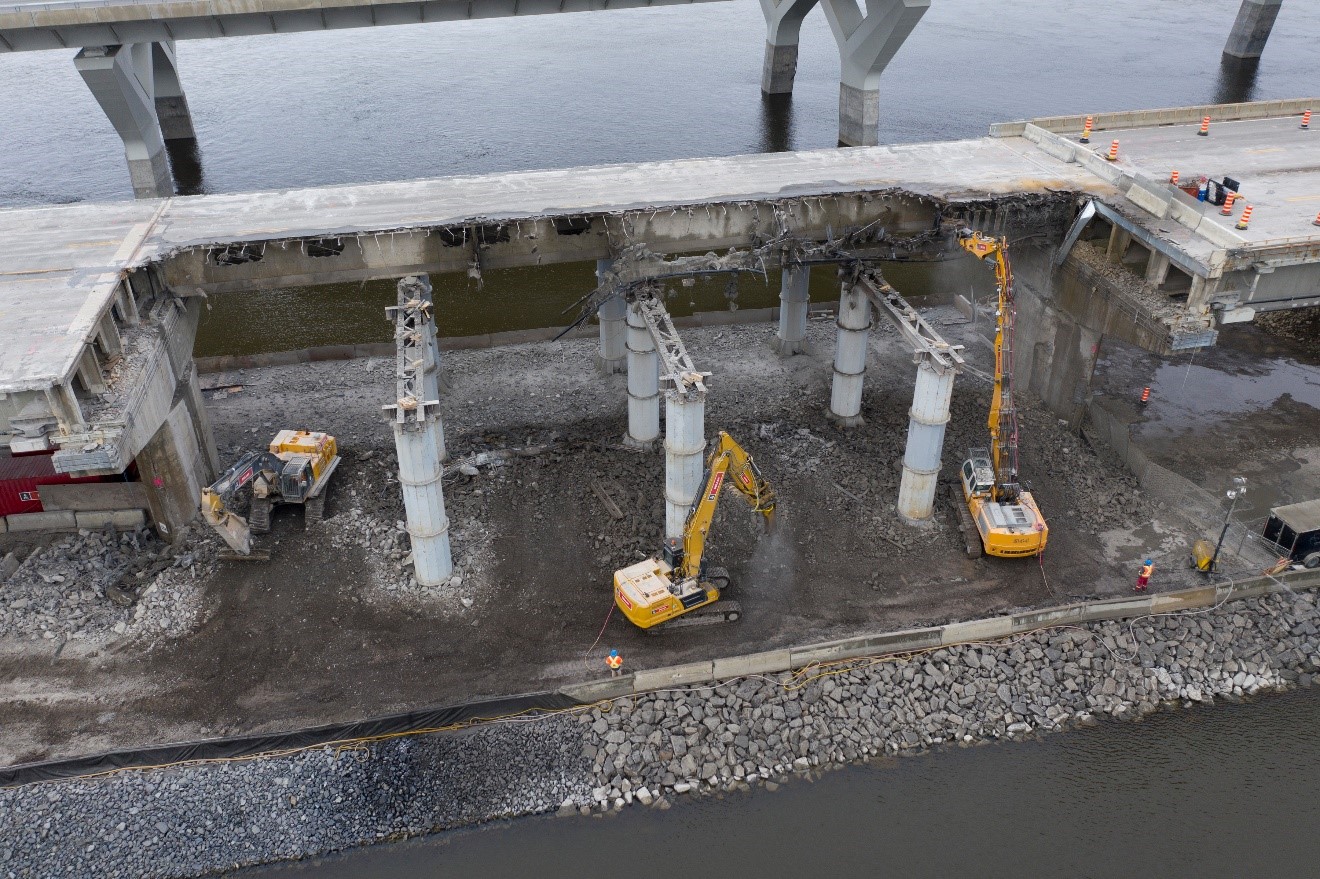
Since Autumn 2020, workers have been dismantling the former Champlain Bridge deck, section by section. (photo: JCCBI)
The “old” Champlain Bridge comprises 17,000 tonnes of steel and 12,000 tonnes of asphalt.
The structure’s concrete elements weigh 253,000 tonnes - the equivalent of 170,000 cars.
JCCBI plans to send parts of the steel superstructure for recasting and repurposing, while the concrete, will be crushed and repurposed as backfill material.

Professor Jean-Philippe Charron and Professor Mahdi Ben Ftima (crédit Denis Bernier)
Using non-invasive methods, the Structural Laboratory team will begin by identifying each of the slabs to gauge the extent of their deterioration and their residual load-bearing capacity.
“Over the years, freeze-thaw cycles and corrosion have likely reduced concrete and rebar performance, which in turn affects the slabs’ capacity to support vehicular loads. Our goal is to determine the extent of the damage,” Professor Charron theorizes.
To test their idea, his team will examine selected slabs by attaching electrodes to the surface, then measuring, at multiple points, the electrical conductivity of the rebar grid embedded in the concrete.
“By compiling all the measurements we gather and performing sophisticated digital analyses, we think we can identify the precise locations of corrosion in the rebar grid. From there, we’ll estimate the residual diameter of the rebar and assess the residual load-bearing capacity of the slabs when experiencing bending and shear,” Professor Charron explains.
The data will also be used to improve predictive digital models developed by Polytechnique Montréal researchers and their CRIB colleagues, eventually enabling them to accurately simulate the behaviour of concrete structures subjected to various exposure conditions.
Further validation of UHPFRC

This initial step is the diagnostics aspect of the work; with the information gathered in this stage in their notebooks, researchers will subsequently attempt to “reinforce” some of the slabs to withstand forces beyond their initial capacity.
To accomplish this particular task, the Structural Laboratory team plans to use a material that they’ve been studying for several years: ultra-high-performance fibre-reinforced concrete, or UHPFRC.
If you ask Professor Charron, he’ll tell you that UHPFRC is the acme of perfection when it comes to concrete. Besides offering four to five times the traction resistance and compressive strength of conventional concrete, the material permits deformation under traction of up to 0.2% without the formation of localized cracking. “We’re talking another dimension,” he says.
Additionally, since UHPFRC is so dense, it’s 100 times more resistant to water and other aggressive and potentially damaging agents such as chlorides and sulfates. Further, if a local microcrack forms and water infiltrates, the consequences for the overall structure will be limited, because this concrete is “self-healing.” The latter feat is achieved thanks to unhydrated cement particles - large quantities of which are trapped inside the concrete -and which react on contact with water to seal fissures.
To accomplish this particular task, the Structural Laboratory team plans to use a material that they’ve been studying for several years: ultra-high-performance fibre-reinforced concrete, or UHPFRC.
If you ask Professor Charron, he’ll tell you that UHPFRC is the acme of perfection when it comes to concrete. Besides offering four to five times the traction resistance and compressive strength of conventional concrete, the material permits deformation under traction of up to 0.2% without the formation of localized cracking. “We’re talking another dimension,” he says.
Additionally, since UHPFRC is so dense, it’s 100 times more resistant to water and other aggressive and potentially damaging agents such as chlorides and sulfates. Further, if a local microcrack forms and water infiltrates, the consequences for the overall structure will be limited, because this concrete is “self-healing.” The latter feat is achieved thanks to unhydrated cement particles - large quantities of which are trapped inside the concrete -and which react on contact with water to seal fissures.
“That property not only makes it an ideal material for performing repairs, but also for reinforcing a structure without adding an extra layer of concrete to the damaged portion. UHPFRC-based repairs can potentially extend the life cycle of our infrastructures by a few dozen years,” explains the RIB-affiliated researcher.
By making repairs with UHPFRC, the research team will attempt to enhance the structural capacity of their former Champlain Bridge slabs beyond their initial as-built capacity under bending and shear stresses. “In recent years, we’ve done this kind of reinforcement on new slabs in the laboratory. Degraded Champlain Bridge slabs will provide us with a unique opportunity to demonstrate UHPFRC’s reinforcement capacity on damaged concrete,” Professor Charron notes.
UHPFRC has been added to some Canadian reinforced-concrete building codes in recent years, and though it’s gaining in popularity among structural engineers, its use remains limited. The validation of UHPFRC reinforcement behaviours expected to result from this project will likely generate positive feedback in the industry and, it’s hoped, will lead to more users adopting the material.
Paris' Stade Jean-Blouin was one of the world's first architectural works designed using UHPFRC. (Photo: dalbera, licence CC 2.0)
WORK delayed due to covid-19
The first Champlain Bridge slabs were originally scheduled to arrive at Polytechnique Montréal in Autumn 2020, but like so many other projects, disassembly work was put on hold because of the pandemic. The slabs are now expected to arrive in Summer and Autumn 2021.
Professor Robert Tremblay (Department of Civil, Geological and Mining Engineering) will also be get a chance to test materials from the “old” Champlain Bridge: in his case, steel sections. However, the superstructure spanning the St. Lawrence Seaway is not slated to be dismantled before Winter 2022, so he’ll have to wait a year before his turn comes to conduct direct studies on steel from the bridge.
FROM CONVENTIONAL CONCRETE... To uhpfrc |
![]() ![]() Rome’s Pantheon, built some 2,000 years ago, has a 43-metre-diameter concrete dome of unreinforced concrete - enduring proof of the ancient Romans’ mastery of advanced building techniques. (Photo : pontfire, licence CC 2.5) The history of cement and concrete begins in early Antiquity. Around 3000 BC, builders in and around Mesopotamia developed various approaches to combining materials and using a binder with the capacity to solidify the mixture. The Egyptians, for example, used a mix of sand and gypsum, to which they added pebbles. Later, the Romans perfected the process. With their mastery of concrete mixing, they were able to build imposing structures like the Pantheon, as well as an entire network of aqueducts. The material saw a new boom in the 19th century with the industrialization of the cement manufacturing process and a number of other innovations. The French, for example, developed an approach whereby concrete was left to harden around a steel framework: the birth of reinforced concrete. In the 20th century, additional techniques were developed and refined, including pre-stressed concrete, which was used for the original Champlain Bridge. In the latter case, concrete was allowed to harden around tensioned steel cables, and the combination of these materials increased the capacity of built structures. Various types of UHPFRC emerged at the end of the century, and have been used mainly in Europe and Asia to design architectural cladding—for example, that of Marseille’s Museum of European and Mediterranean Civilisations—and bridges. In Québec, UHPFRC use has begun more recently, such on projects like Montréal’s Isabey-Darnley pedestrian overpass, which has a slab of UHPFRC designed by Professor Charron’s team |
Learn more
Professor Jean-Philippe Charron’s expertise
Professor Mahdi Ben Ftima's expertise
Groupe de recherche en Génie des Structures's expertise
Department of Civil, Geological and Mining Engineering website
Comments
Commenter
* champs obligatoire